Your shopping cart is empty.
Harnessing the Power of Data to Drive Performance & Fleet Management
Posted in Sustainability,  Productivity,  Best Practices,  Robotic Cleaning Machines, 
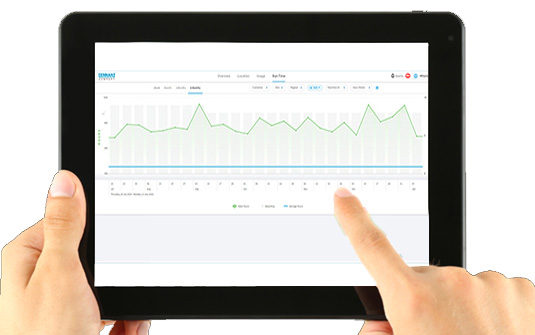
The robust usage data collected by today’s asset management solutions provides an instant snapshot of fleet performance. But this data is just the starting point — the true potential of these solutions lies in the myriad ways you can leverage this data to develop new insights, identify opportunities and drive differentiators.
Here are five critical steps to begin turning reliable data into powerful results:
1. Collect Usage Data to Drive Consistent Cleaning
At the most basic level, cleaning service businesses need an objective means to verify their operators are getting the job done, meeting cleaning contract requirements and delivering value to their customers. An asset management solution enables objective verification of compliance with cleaning contracts.
Looking at machine usage data, fleet and site managers can monitor average daily usage and drill down to examine specific sites or machines to ensure consistent compliance with cleaning contracts across every site and every machine.
Customers remember the rare bad experience more than years of reliable cleaning, so consistency is key for healthy customer relationships. Monitoring usage data, fleet managers can ensure every site receives consistent cleaning— day in and day out — driving the dependability of your cleaning services.
2. Identify opportunities to improve productivity & reduce labour costs
Labour has always accounted for a major portion of BSC operating costs. Finding opportunities to increase your labour productivity and reduce labour-related costs can create significant cost savings. By looking at machine usage data, BSCs can identify specific sites — or even specific machines and operators — that show below-average productivity. These outliers are prime opportunities to provide additional operator training, ensuring staff are proficient in operating cleaning equipment and familiar with best practices. This enhanced training boosts operator productivity to improve overall fleet efficiency.
3. Ensure health & safety benefits to reduce labour costs
Ensuring optimal staff training not only improves overall productivity — it can reduce health and safety incidents to keep your staff safe and further reduce labour costs. In addition, many BSCs are now recognising the value of sustainable cleaning technologies that reduce or eliminate the need for harsh cleaning chemicals and staff exposure to these potentially harmful materials, thereby mitigating health and safety risks for machine operators and other cleaning staff.
Comprehensive fleet metrics enable fleet managers to ensure that these safe and sustainable cleaning technologies are being used —and used properly — to maximize health and safety benefits and prevent costly safety incidents.
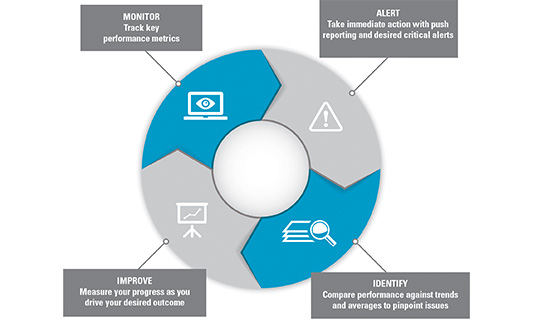
Tennant fleet management life cycle is simple and easy to implement.
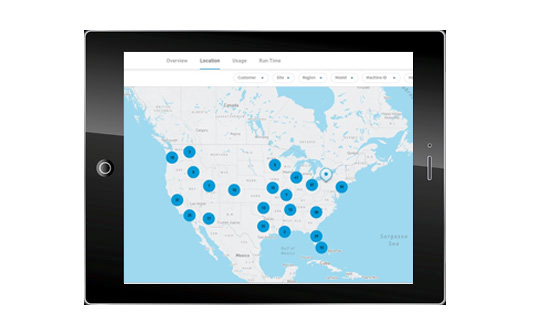
Capture metrics and get insights to achieve control of your cleaning operations and drive measurable results — from maximising productivity to optimising execution.
4. Leverage usage data to optimize fleet size & deployment
How do you know you have the right size cleaning fleet for your needs — and how do you ensure that your cleaning resources are where they are most needed? Under-utilised resources cut into your bottom line, but overworked machines and operators come with costly breakdowns and the risk of health and safety incidents. That's where the importance of data is vital in the cleaning industry and comes into play. Finding the right balance is a critical and incredibly difficult challenge for any fleet manager, as they oversee multiple sites and contracts, and manage the dynamic needs of each site. The usage data provided by an asset management solution delivers the information necessary to make these decisions.
Equipped with comprehensive fleet metrics including detailed machine usage, fleet managers can drive consistent cleaning performance and demonstrate exceptional cleaning value, creating a compelling differentiator to win cleaning contracts with existing and new customers. This same powerful data empowers fleet managers to optimise the deployment of cleaning resources to maximise cleaning efficiency, reduce labour costs by providing productivity-boosting training and decreasing costly health and safety incidents, and ensure less operator misuse to protect their equipment investment. Leveraging the robust potential of an asset management solution, the forward-thinking cleaning service organisation can successfully and simultaneously maximize bottom-line margins and enable top-line growth to drive significant profitability gains.
5. Analyse your data — find your opportunities for improvement
For the operationally perfect cleaning business, an asset management solution simply provides a tool for demonstrating that perfection through data. But in the real world, even the most efficient cleaning fleets have flaws — and an asset management solution empowers you to identify these opportunities for improvement to continually enhance your cleaning operations. This continuous improvement process begins with setting a baseline for your current performance. Monitoring fleet metrics like machine usage, you can quickly establish benchmarks against which to measure your improvement efforts.
In most multi-site cleaning operations, a few leading sites will emerge — sites showing higher performance and/or lower cost-to-clean than the fleet averages. These high performers can be used as models for creating best practices, investigating differences in operator training, management/supervision, equipment and product usage, and identifying those practices that contribute to improved performance and/or reduced costs.
Continuous Improvement Through Better Reporting
Equipped with comprehensive fleet metrics including detailed machine usage, fleet managers can drive consistent cleaning performance and demonstrate exceptional cleaning value, creating a compelling differentiator to win cleaning contracts with existing and new customers. This same powerful data empowers fleet managers to optimise the deployment of cleaning resources to maximise cleaning efficiency, reduce labour costs by providing productivity-boosting training and decreasing costly health and safety incidents, and ensure less operator misuse to protect their equipment investment. Leveraging the robust potential of an asset management solution, the forward-thinking cleaning service organisation can successfully and simultaneously maximise bottom-line margins and enable top-line growth to drive significant profitability gains.
RELATED LINKS
