Your shopping cart is empty.
Cleaning is More than Making Things Look Nice
Posted in Industry News & Trends, 
Health, Safety, and Cleaning Intersect
Tennant’s new guide, The Dirt on Floor Care for Large Facilities, offers information on efficient, cost-effective maintenance.
The following text is Chapter 1 of the guide, “Where Health, Safety, and Cleaning Intersect.”
We’re starting to see attitudes shift from cleaning for appearance to cleaning for health. Facility managers have begun to take notice of infectious diseases and contaminants that raise flags for health care professionals and public officials.
Benefits of Cleaning for Health
Cleaning for Health produces noticeably cleaner buildings that customers, employees and visitors typically equate with a well-managed business. But the real impact of Cleaning for Health comes from reducing dust, chemical residues and bacteria from the surfaces we encounter every day.
Improving Indoor Air Quality
We spend as much as 90 percent of our time indoors, often in poor indoor air quality (IAQ) environments. It’s estimated we lose 150 million work days each year due to poor indoor air quality, with related health care costs reaching more than $15 billion annually.1
Over the past 30 years, manufacturers of carpeting, flooring, paints and building materials have reduced the gases their products emit into indoor environments. In addition, most buildings are now smoke-free, which has certainly improved IAQ. The JanSan industry has also played a vital role in further reducing IAQ problems by using cleaning products with fewer harsh chemicals.
Environmentally Preferable Products
We can expect more JanSan manufacturers to produce more sustainable cleaning chemicals in the future as a way to help minimize their environmental impact.
What to look for when selecting sustainable cleaning products:
- Engineered water products like hydrogen peroxide, ozone, and other on-site generated solutions
- Products with low or no odors or fragrances
- Water-based (not solvent-based) cleaning chemicals
- Telemetry on equipment, providing actionable data for improving energy efficiency
- Autonomous floor care or robots that maximize productivity, increase efficiency and optimize safety
Reducing Exposure to Volatile Organic Compounds
Volatile Organic Compounds (VOCs), including fragrances often found in cleaning products, can contribute to poor indoor air quality and can irritate individuals with chemical sensitivities or asthma.
To limit VOC exposure in your facility:
- Check your daily use cleaning chemicals and choose products without added fragrances
- Avoid using air fresheners or other products that use artificial fragrances to mask unpleasant odors
- Minimize the use of solvent-based cleaners – save them for tasks where gentler cleaners aren’t effective, and make sure any area where they’re used is well ventilated
Using products with fewer harsh or volatile ingredients is definitely a step in the right direction, but ultimately, it’s the cleaning process that has the biggest impact on the health of a building and its occupants.
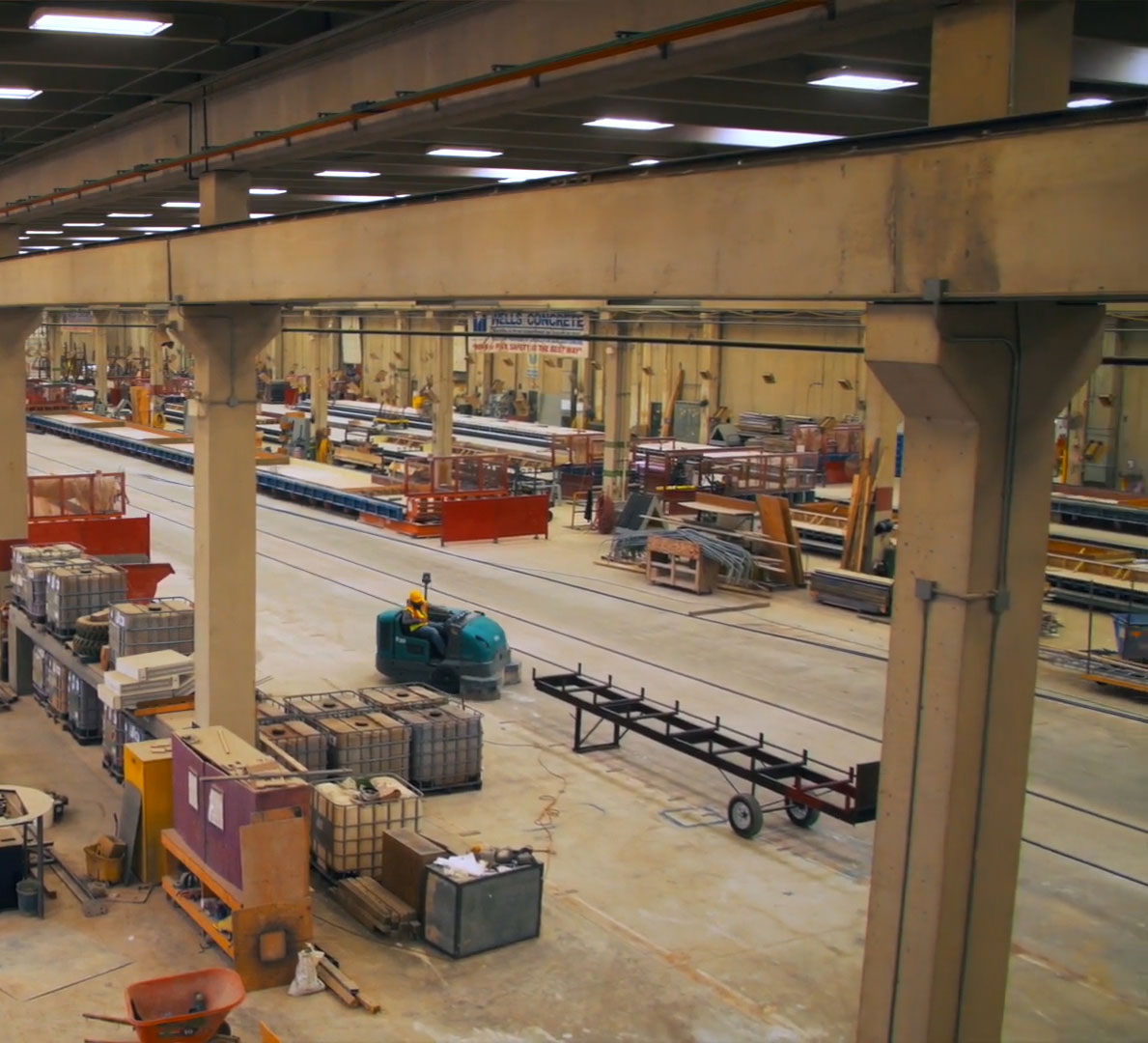
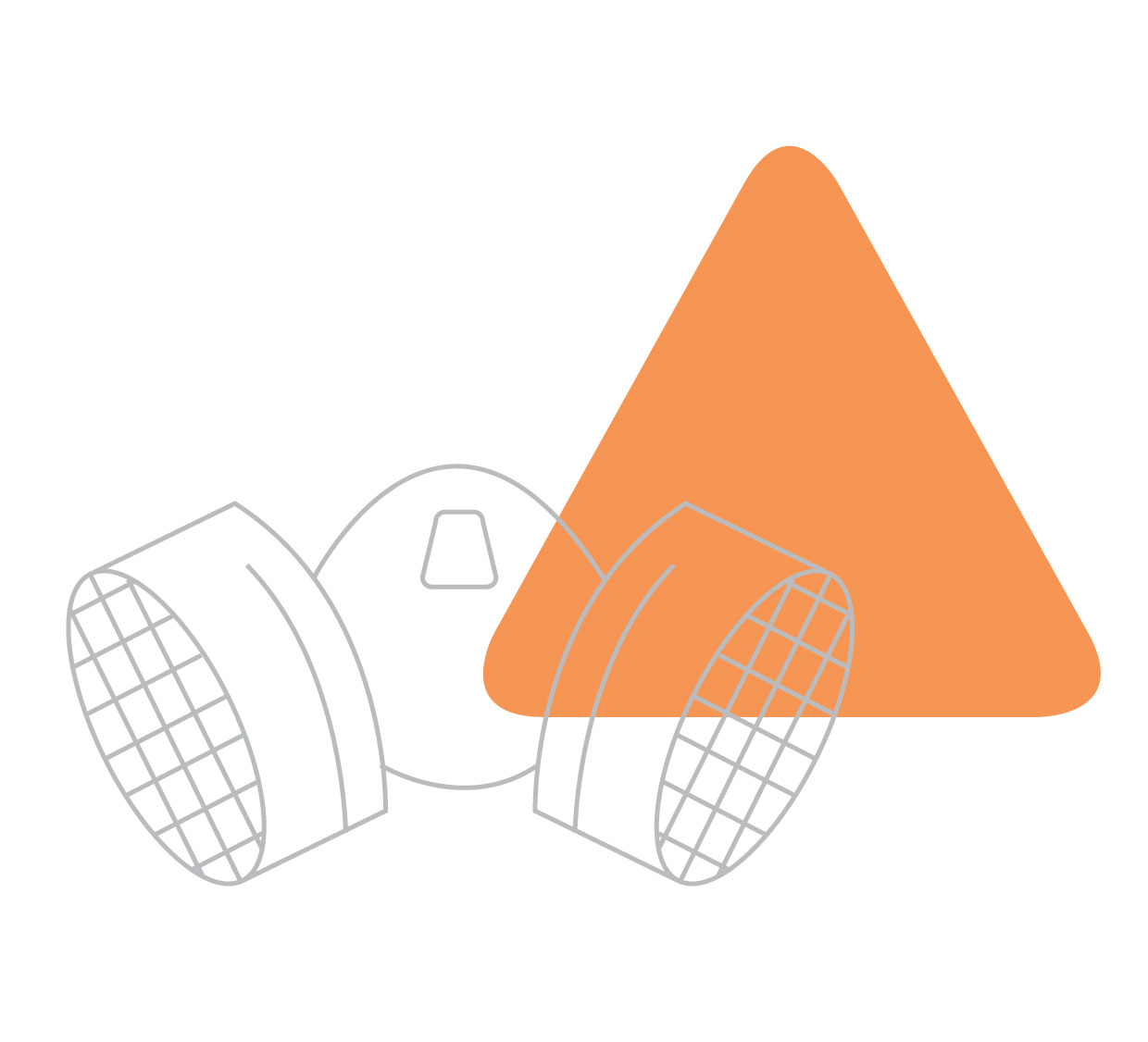
