Your shopping cart is empty.
How to Reduce Labor Costs in Your Cleaning Budget
A Proactive Approach to Cutting Labor Costs in Manufacturing
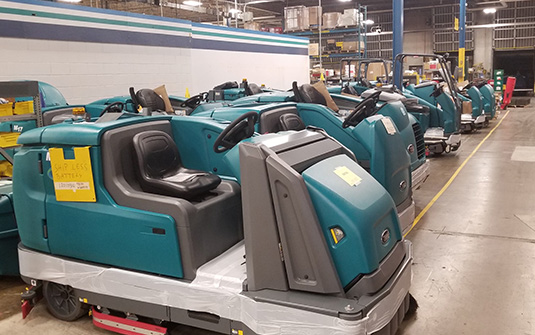
There is one topic on the mind of every facility manager’s mind, no matter what type of facility or cleaning budget they are working with, and that’s the cost of labor. Up to 50%, and often more, of a cleaning budget will go toward labor.
Because it’s one of the most significant expenses, labor is frequently targeted as an area to identify potential cost reductions. At the same time, because it’s one of the most important assets, companies don’t want that cost reduction to come at the expense of a motivated, efficient team.
The good news is that reducing labor costs is possible. The toolkit provided below is designed to help your facility fine tune its cleaning program, from HR policies to equipment investments, toward the common goal of reducing the amount of money spent on labor.
HR Toolkit for Reducing Labor Costs
Combine virtual training sessions with physical training materials. Technology helps get the most out of training programs, and many of the most robust training programs are implemented virtually. For example, on-demand training videos walk through the steps of a maintenance routine and virtual training allows workers to access training from anywhere, at their own pace. Depending on the task, a training tool can be as straight-forward as a wall chart or a laminated checklist. The key is to identify opportunities where a skill gap can prevent an employee from successfully completing a task, and then finding an easy-to-understand method to provide training for that skill.
Adopt a culture of training. Opportunities to look beyond a simple training program and adopt a culture of support, education and recognition will pay dividends in labor cost reduction. Training is about more than just setting up sessions for your workforce. Managers should have a trainer mindset, using opportunities for education whenever they arise. Observe your operators in action to make sure they’re handling machines properly. This will help keep your equipment from breaking down prematurely, and will allow you to correct operators in the moment, breaking bad habits before they form.
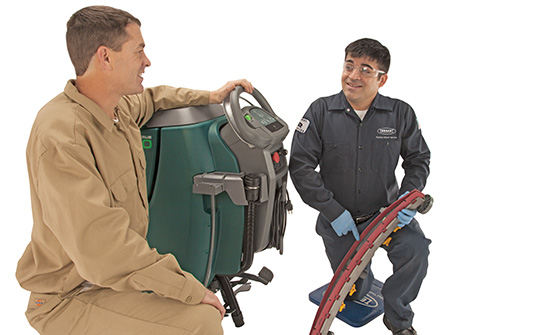
On the job training and job shadowing is an effective way to help reduce cost and a sound alternative to paid training when appropriate.
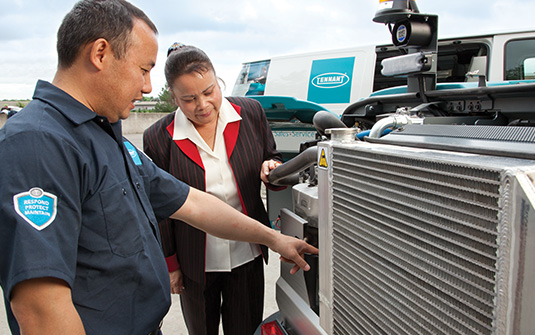
Helping to educate your customers helps them to understand the importance of equipment manitenance to save on cost for full machine replacement.
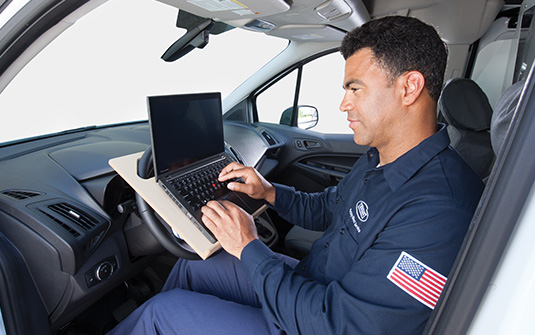
Virtual training and webinars are a great way to minimize cost on things like travel and lodging for your cleaning staff.
Reduce employee turnover. When an employee leaves, the costs add up. There’s the loss of productivity, the overtime pay to cover for it, and the expense to recruit, hire and train a replacement. Often, the cycle repeats itself. Anything you can do to increase employee engagement—from building a robust training program to offering opportunities for advancement and recognition—will help reduce turnover in your workforce, saving money in the long run.
Prepare for gaps in staffing. To account for the inevitable turnover that your workforce will encounter, make sure to cross train employees so that they may complete many different cleaning tasks and operate your entire fleet of machinery. This will help prevent bottlenecks in your cleaning program and ensure that employees can step in for those who leave, whether for good or temporarily.
Attract and retain younger workers. As earlier generations of cleaning professionals retire out of the labor market, the cleaning industry has had to shift to attract younger workers to the job. According to SHRM, Gen Zers now make up 36% of the workforce, so it’s imperative to align your business culture with their perspective and needs. For example, these younger workers value training and development, citing these initiatives as the main reasons they stay with a job. To make sure the younger team members you hire see the job as a long-term career path, it's important to have a robust training program and opportunities for development and advancement.
Enhance safety. Your employees are valued assets. Make sure you’re providing them a clean, healthy and safe work environment. Implementing best-in-class safety protocols and equipment with built-in safety features, like back-up alarms, lights, and properly installed squeegees for water pick-up can help reduce the chance of accidents and costly workers compensation claims.
Reduce overtime. It may be tempting to pay overtime to get a job done or cover for a staffing shortage, but overtime costs add up quickly. Staffing and HR departments should focus on strategies to reduce overtime work, such as adding part-time staff, finding temporary workers and maximizing efficiencies.
Having part-time staff or a source for temporary workers can strengthen your capabilities, and reduce your payroll. Using a simple time and attendance app or tool will also avoid stolen time, which is often an unintentional consequence of lax timekeeping. Have your employees use a simple system to clock in and out so you can be sure you aren’t paying more than time worked. Newer tools and apps are very efficient, include facial recognition software and can be synced to payroll providers.
A Guide to Choosing Equipment that Reduces Labor Costs
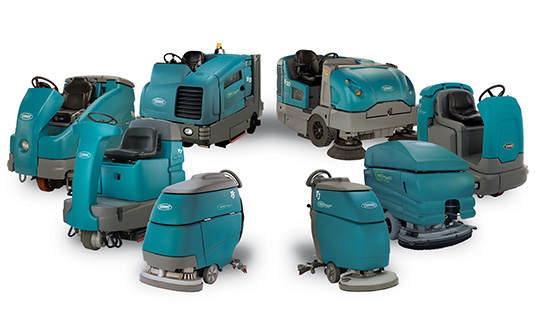
When it comes to cutting labor costs, there must be a balance between investing in efficient technologies and streamlining your workers’ jobs. The industry is constantly changing, but the goal for most new technology is aligned with maximizing worker efficiency. Innovative new technology and equipment can simplify and streamline cleaning processes, and provide a quick return on investment. Streamlined cleaning equipment can provide consistency, efficiency and ease of use and maintenance, making the ROI in terms of labor costs clear.
Consolidate products + streamline your fleet. Buying larger quantities of equipment from a single supplier can often result in a quantity discount, but the savings don’t stop there. Having a fleet of equipment in the same family will streamline your training programs and make your workers’ jobs easier and more efficient. When you have a group of products from the same family, operators don’t have to learn multiple processes for cleaning.
Robotic floor cleaners create labor efficiencies and cleaning consistency. Robotic floor cleaning equipment works alongside your cleaning staff, methodically and consistently handling essential floor cleaning while your staff simultaneously does other core cleaning tasks. Robotic floor cleaners lift the burden of time-consuming and monotonous cleaning tasks, allowing your staff to focus on work that only a human can do — including regular deep cleaning, targeted cleaning and facility care. By shifting unengaging work to robotic floor cleaners, cleaning staff can take on different responsibilities — from expanding their skillset to include robot training and management, to inventory control or customer service.
Capture data to optimize your cleaning program. Robotic floor cleaners feature integrated data capture technology that delivers real-time performance and utilization tracking. You can verify cleaning has been done — and done correctly — to deliver proof of value, support compliance and ultimately drive better overall cleaning performance. By increasing staff engagement, robotic floor cleaners can help mitigate staff turnover and even potentially reduce the costs of equipment damage from operator error during manual operation.
