Your shopping cart is empty.
The Importance of a Site Needs Analysis
Posted in Industry News & Trends, 
Putting the Numbers to Work
Tennant’s new guide, The Dirt on Floor Care for Large Facilities, offers information on efficient, cost-effective maintenance.
The following text is Chapter 3 of the guide, “The Importance of a Site Needs Analysis: Putting the Numbers to Work.”
Once you understand the fundamentals and tools involved in conducting a site needs analysis, you’ll be able to get more out of your workforce.
Facility managers need to be prepared to justify staffing needs. This includes having accurate answers to the following questions:
- How long does it take to complete a task?
- How does adjusting the frequency of the task affect cost and outcome?
- How would a change in square footage affect the budget?
- How would a change in wages affect the budget?
- What’s the best practice for completing a task at the lowest possible cost, without affecting the outcome?
The process of workloading answers these questions by establishing a scope of work, staffing levels and what it costs to perform the work. Once you understand the fundamentals and tools involved in conducting a site needs analysis, also called “workloading,” you’ll be able to get more out of your workforce.
The Workloading Process
Guessing how many hours or employees it takes to clean an area or building is neither reliable nor accurate. Even if your estimates appear correct, they can’t be verified or defended. The four-step workloading process allows you to do both.
STEP 1
Take Inventory of Your Space
- Determine the total amount of cleanable space (not gross square footage) in your facility using the architectural drawings or a laser measuring device
- Categorize each type of area to determine the square footage of each cleanable surface (for example, 50,000 square feet of manufacturing space)
- Make note of cleanable objects—manufacturing stations, storage areas, trash barrels, or restroom fixtures—in each space
STEP 2
Create a Scope of Work
- Define the tasks needed in each area type
- Determine the desired appearance, germ transmission, manufacturing equipment life cycle, cleanliness and health and safety of building workers, occupants, and visitors
- Calculate the number of times each task needs to be performed per year
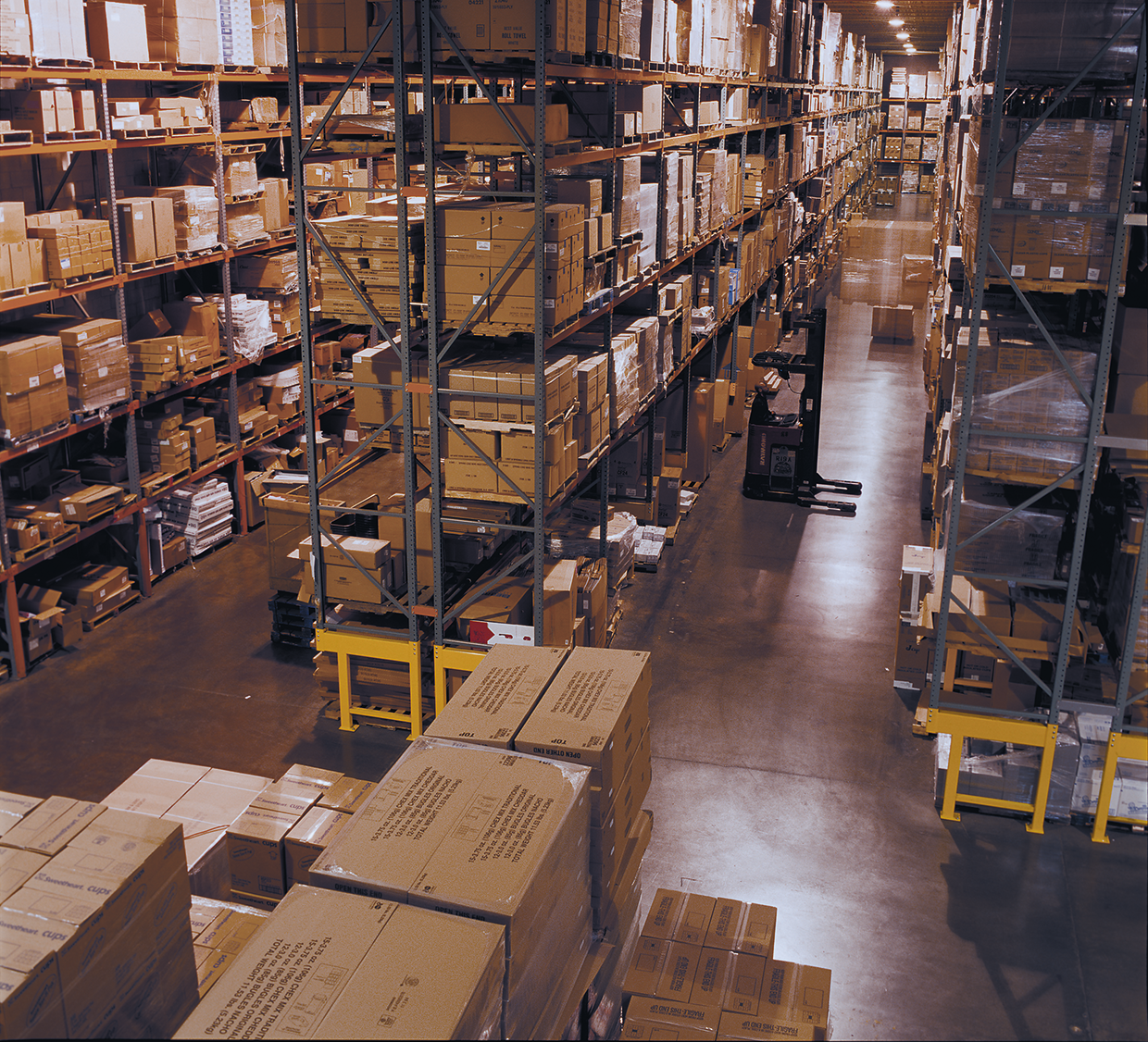
